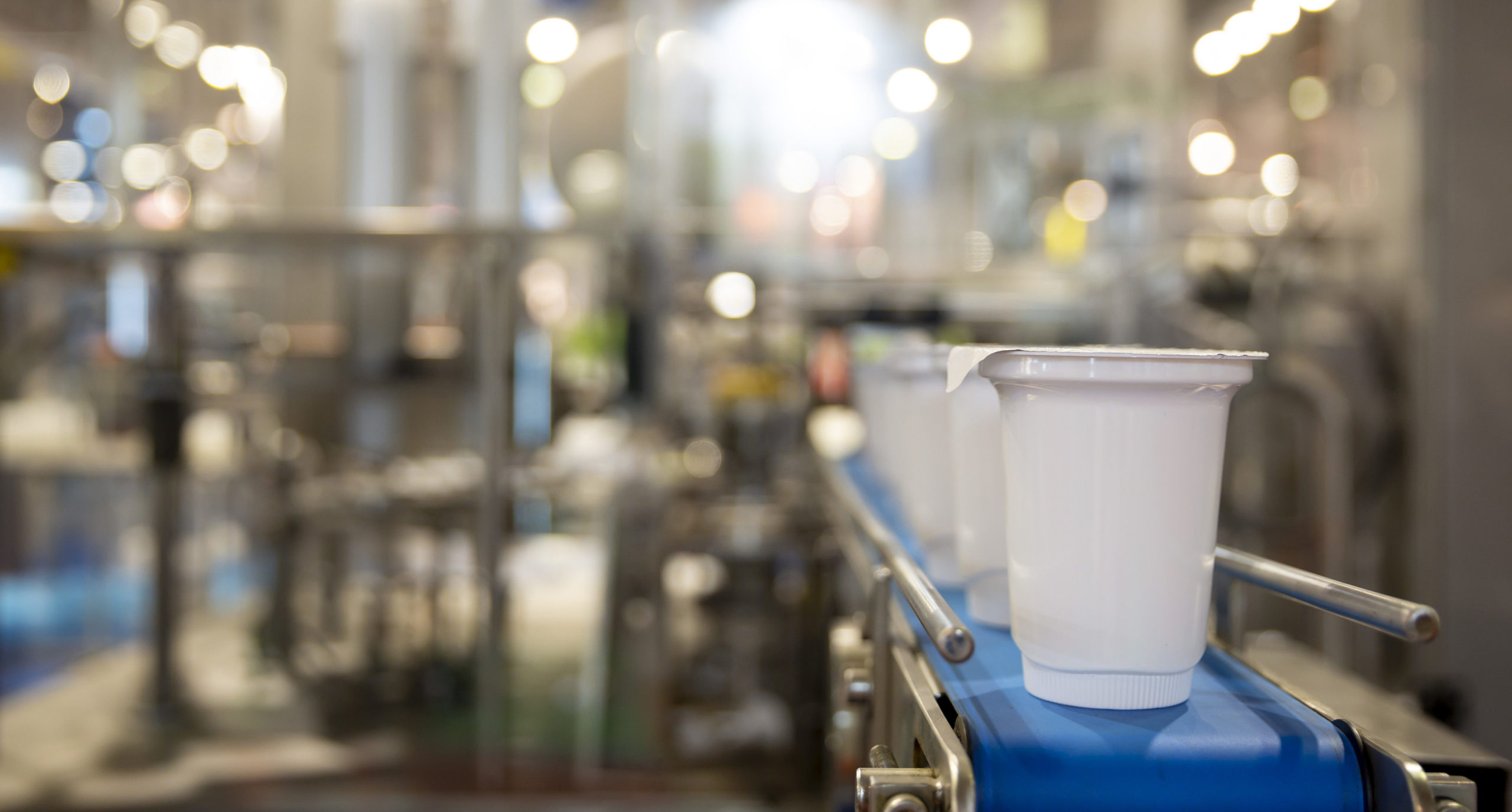
7 Reasons Why Food
Producers Should
Inspect Primary Packaged
Products
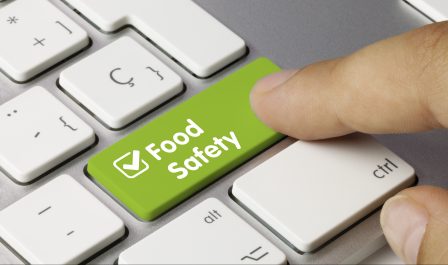
7 Reasons Why Food Producers Should Inspect Primary Packaged Products
Sometimes, food producers might consider the implementation of X-ray inspection to be costly or complex and therefore be tempted to install X-ray systems only for secondary packaging inspection or early on for the bulk/unpacked production inspection. These options might sound initially attractive but let us explain the 7 reasons and benefits that food producers get when placing the X-ray inspection for primary packaged products.
1. Product safety – This is usually the main reason to implement X-ray inspection in the first place, and only by inspecting single packaged products can we maximize product safety. When the products are packaged and sealed, there is no possibility for further contamination after the inspection. Also, retail chains and consumers often expect that the inspection should take place after packaging.
2. Improved accuracy – Inspecting large boxes with multiple products on top of each other inside is not as accurate compared to the detection accuracy that can be achieved when the inspection is done on single packaged food products. This results in the detection of smaller contaminants but also decreases the amount of possible false rejects caused by variations in the X-ray image at bulk or secondary packaging.
3. Quality control functions – X-ray inspection offers valuable quality control functions that help food producers to improve the overall quality of their products. These functions analyze the content of packaged products for any quality defects, such as misshaped, broken, or missing parts of the products, and remove them from the production. This helps to decrease the number of consumer reclamations and therefore builds a stronger food brand. These functions provide the best value at primary packaging.
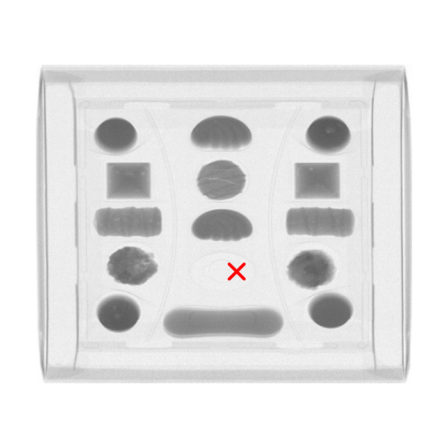
4. Traceability – Inspecting single packaged food products also increases the traceability of the production process significantly. The X-ray system is able to track products going through the system, trace contaminations, calculate pack rate and time-stamp rejections. Food producers have the option to save each X-ray image that was taken and present proof of the complete production batch whenever needed.
5. Less waste – Primary packaging inspection supports the goal of more sustainable production by reducing waste in case of contamination detection. If contamination is detected, the system will only reject the single packaged product and not the whole carton of products or part of bulk flow, thus creating less waste.
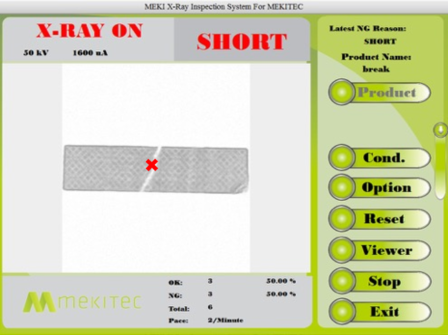
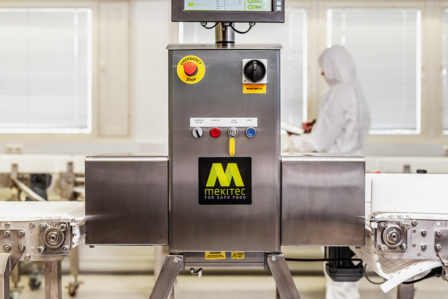
6. Smaller size, cost, and consumption – Inspecting primary packaged products usually requires lower X-ray power, which enables the systems to be smaller in size and less costly. Lower power consumption can also help to extend the lifetime of the critical parts, i.e. X-ray generator and detector.
7. Production efficiency – Having only one or a few X-ray systems for unpacked/secondary packaging increases the risk of having a lower production efficiency in case there are any failures with the system. Primary packaging inspection offers the possibility to direct the production through multiple packaging lines and reduces the chances of losing the total production efficiency.
When choosing the most suitable inspection solution for your food production, it is important to consider all these factors and ensure that the system provides the most value in terms of performance (e.g. detection accuracy, additional quality control functions, and production efficiency) and lifetime costs.
free white paper
More Information
Fill in the form to download our white paper about primary packaging inspection and learn how inspecting single packaged products can tremendously improve the foreign object detection rate, reduce waste and more.
More about X-ray systems
