
Food traceability & transparency
achieved by X-ray inspection
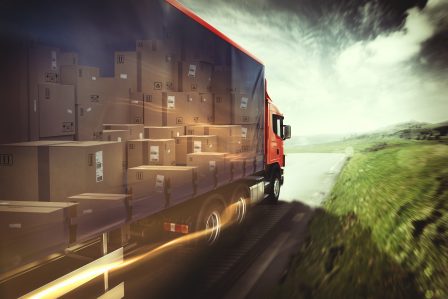
Food traceability as a part of food safety and quality control
Food traceability means the ability to track any food or its substance that will be used for consumption through the steps of production, processing, and delivery. Ideally, a proper food traceability system allows the food manufacturers to locate and identify a food product at any step of the production or supply chain.
Food traceability is vital for increasing operational performance because it supports manufacturers in improving efficiency by identifying mistakes in the manufacturing process and validating the consequences of measures taken to increase efficiency. Food traceability can also be used to assure customers that the products are safe and ethically produced. When necessary, traceability can also help food producers to recall specific products from a certain production batch more precisely and even proactively.
Tracing the source of food contamination within the supply chain is essential to food safety. In a previous blog, we wrote about food traceability being one of the top five food trends of 2019 according to IFIC (International Food Information Council). The article in Food Processing Magazine shows that in 2021 food traceability still is an essential factor in every food safety system and is becoming more digital and automated every year.
Read more about food traceability from our article: traceability in the food industry.
What are the benefits of food traceability?
Consumers are more and more interested in the quality, origin, ethics, and contents of the food they buy. This gives an advantage for food companies with transparent food traceability systems in place.
The ability to track food along the manufacturing and supply chain is crucial for consumer safety and brand loyalty since it allows food companies to continue developing and taking corrective actions in a safe way, even if a problem or contamination is identified. This helps to prevent contaminated products from reaching consumers as the hazard is detected early in the food production process with a proper quality control and food traceability system.
Food traceability helps producers to:
-
- Ensure product quality
- Improve the production and supply chain processes and verify the improved results
- Identify the source of a quality issue or safety hazard
- Meet and exceed the requirements of local and global regulations
- Promote transparency and safe food
- Strengthen and maintain consumer trust
- Protect the brand image
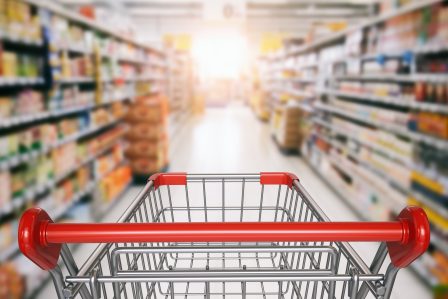
Transforming the CCP into a food traceability point
In the past, critical control points have had a limited part to play in the traceability chain as the previously used technologies have provided very little data to improve traceability. Today, by using X-ray technology CCPs to inspect food products on a pack-for-pack level the food traceability can be improved to include crucial data such as individual X-ray images of each product.
With the primary packaging X-ray inspection and its food traceability function producers can:
- Gather and store data and X-ray images
- Transform the CCP into a food traceability point
- Prove and ensure the safety and quality of the final individual products
- Perform highly targeted recalls if required for any reason
The ability to gather data and store images of all products gives a completely different view of production and food traceability. It can truly transform the CCP into a new traceability point in the company’s traceability chain. It can even work as proof of the safety and quality of the final individual products. With this kind of insurance, the producer can easily go back and see exactly what was produced if there is a claim of any products from a certain batch.
Product recall is a rare but unwanted situation to have and it always creates a lot of different types of damages. If there is a need to perform such a recall; X-ray CCP combined with food traceability can make all of this much more targeted and faster. The increased efficiency in finding the actual problem enables producers to better identify the batches that are okay and the ones that are not. As we all know, speed is always of the essence when it comes to recalls.
Such a targeted recall is a fairly new thing to have. Producers today go even further to ensure safety by implementing these food traceability X-ray systems upgraded with the latest rejection confirmation systems to guarantee that a specific contaminated product that was detected and recorded in the system is rejected into the rejection bin where it can be found as proof.
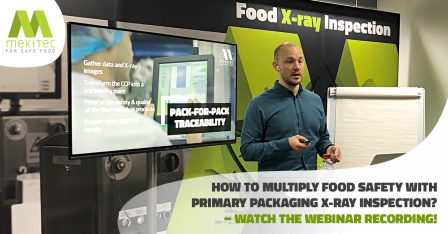
LEARN THE NEW WAY OF FOOD SAFETY
Click the button below and sign up for the “Multiply food safety with primary packaging X-ray inspection” webinar recording to find out more about traceability among other benefits of primary packaging.
Introduction to Primary Packaging X-ray InspectionHow to achieve full food traceability with the Mekitec X-ray imaging system?
Food producers all over the world are implementing effective food traceability solutions to strengthen their businesses, improve product quality and safety, increase efficiency, completely avoid or ease recalls, and ultimately build consumer loyalty and trust.
Compared to other technologies, with X-ray primary packaging inspection food producers can achieve full food traceability and gather more data about:
-
- Incoming and outcoming products
- Rejection rates and reasons
- Timestamps of different products/batches combined with their actual X-ray image
- Differences between shifts, recipes, and more
The primary packaging X-ray inspection together with its modern food traceability features guarantee full food traceability and HACCP compliance, as explained in one of our blogs. The implementation of the Mekitec food X-ray quality control system makes it possible to get better detection rates of contaminations combined with full traceability and additional quality functions. All of this is done to increase inspection performance, reduce investment expenses, and provide the best value.
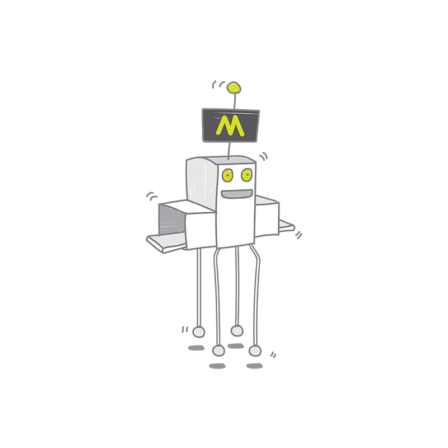
How to Level Up Your Product Safety?
The overall quality of products is now more important to consumers than ever before. We wrote this eBook to help your company choose the best solution for a Critical Control Point and keep your customers happy.
After reading this eBook you will know:
- what is expected from Critical Control Points nowadays
- how to choose an inspection system that brings the most value for your business
- why you too should inspect primary packaged products and how it improves the detection performance compared to any other inspection method
- how to reduce the number of consumer complaints and build a stronger food brand
Fill in the form and you will receive the complete eBook into your inbox!
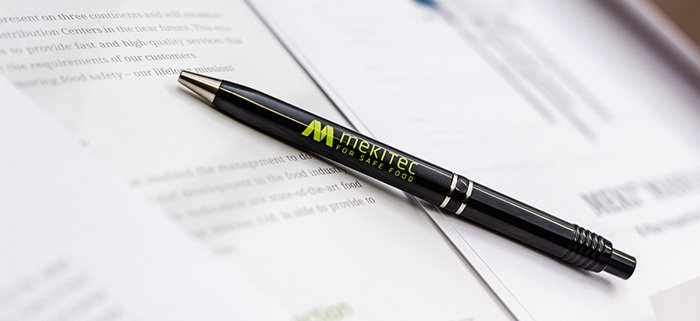