Transform Your Liquid Food Packaging Inspection with SIDEMEKI
As a food and beverage producer, you know that product quality is paramount to the success of your business. Ensuring the best detection performance for your liquid food packaging is crucial, and SIDEMEKI is here to help you achieve that goal.
First, let’s talk about exclusivity. With SIDEMEKI, you gain access to a “side-shooting” X-ray system that provides increased detection accuracy and fewer false rejections for taller-than-wider food products. This unique system is designed to eliminate the risk of physical contaminations, ensuring product safety and brand protection. With our cutting-edge Cap Inspection and fill-level inspection functions, you can take your liquid food packaging inspection to the next level.
Often in the liquid and drink industries, different sieve nets and other types of filtering equipment are used to ensure that there are no physical contaminations in the bulk production before the raw material is processed and eventually packaged. However, the nets and other processing equipment can possess a contamination risk and that is why liquid and beverage producers should always inspect their final, packaged products before they are delivered to retailers and consumers.
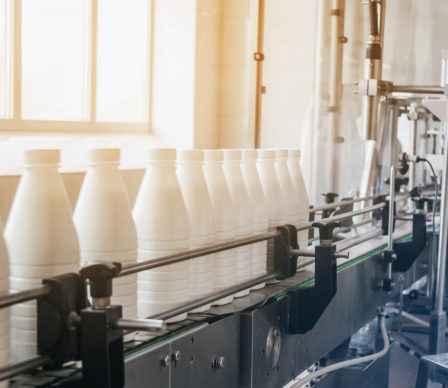
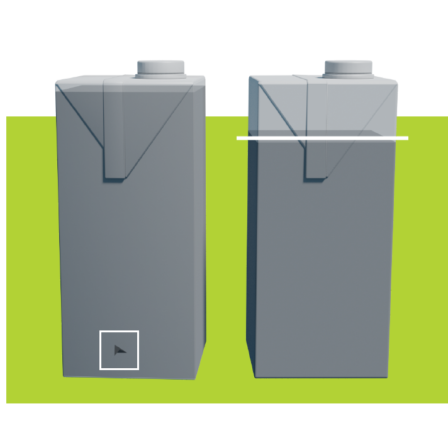
Unlike with ready-to-eat foods and snacks, drinks and other liquid foods are consumed without chewing. This makes it crucial to ensure that even the smallest foreign objects are detected to eliminate the risk of these contaminants causing harm to the consumers.
Inspecting these taller food products with a “side-shooting” X-ray system, liquid and beverage producers are able to not only get the best detection performance but also benefit from quality inspection features that are specifically designed for the liquid applications. The system creates and analyzes a grayscale image of the complete food product in order to identify any anomalies within the product or packaging. These anomalies include foreign contaminants, low fill levels, and open seals or caps, to mention a few. The quality inspection features provide better food safety (by inspecting that all seals or caps are properly closed) and assure product integrity and brand protection (by monitoring of e.g. fill level).
Tall Cartons and PET Bottles Require More from the Production Equipment
Let’s talk about efficiency. Traditional top-down X-ray systems may not be sufficient, and detecting defects from the thinnest side of the product is challenging. But with SIDEMEKI you can inspect your liquid food packaging with ease, even in the most challenging production environments. Our product guides and smooth transfers between different conveyors guarantee a smooth production flow, minimizing the risk of downtime and jams.
The unique challenge with e.g. bottle production lines is the production flow, which somewhat differs from other food production lines because the products are tall but narrow, and therefore more sensitive to fall over and lead to production flow downtime by causing a jam. That is why it is so important to design the equipment for these specific production conditions in order to guarantee smooth inspection without interference. Product guides, as well as smooth transfers between different conveyors, are the key to guarantee a smooth production flow in these industries.
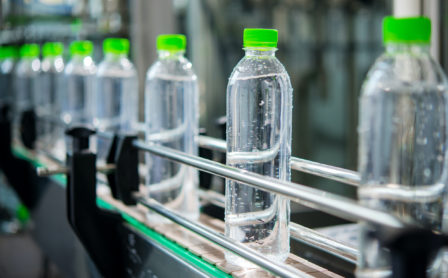
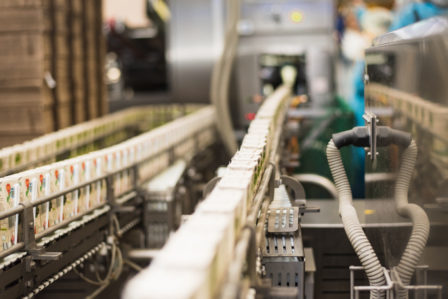
Inspect Tall Cartons and PET Bottles without Compromises
To ensure the safety and quality of drinks, beverages, and liquids packaged in tall bottles and cartons, food and beverage producers can nowadays choose to have an X-ray system with one or two generators. This enables multiple imaging angles for the food products and having a sharp image of both the bottom and top part, providing increased detection accuracy and less false rejections, which could result from one blurry X-ray image.
If the producers choose to implement a food inspection system with only one X-ray generator, it means that they also need to choose the main focal point for the inspection, i.e. to inspect hazardous physical contaminants that usually end up in the bottom part of the product, or to inspect quality defects, such as fill level or a missing cap, that are located on the top of the product.
Sometimes when the food or beverage packaging is not too tall, you can manage to do both by placing the focal point on the top or bottom of the product. When doing so, food producers may need to make compromises when it comes to the detection rates of foreign contaminants or false rejection rates, and in many cases that is not feasible.
For example, in the dairy industry, it is necessary to inspect the sealing integrity of the carton package while also ensuring that the products are free from any physical contaminants. Also, many liquid and drink products are packaged in PET bottles, where it is crucial to inspect headspace and cap presence, especially if the packaging does not allow the use of any visual inspection systems.
When food producers choose to implement an inspection system with two X-ray generators instead of one, they can ensure the best detection and lowest false reject rates for the complete product as the system can use the sharpest possible image for the analysis. Meaning, that the system is able to detect any quality defects and the smallest foreign objects, whether they are on top, middle, or at the bottom of the product.
the datasheet
Why Choose SIDEMEKI to Inspect Tall Cartons and PET Bottles?
Don’t settle for traditional top-down X-ray systems that limit your liquid food packaging inspection performance. Transform your business with SIDEMEKI and take your liquid food packaging inspection to the next level. Contact us today to learn more about how we can help you elevate your liquid food packaging inspection and ensure the best detection performance for your products.
To see how SIDEMEKI fits into your operational needs, simply fill in the enclosed form and you will receive the system datasheet to your inbox.
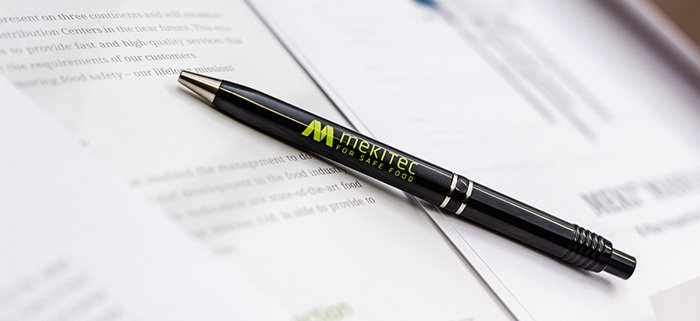